Custom Rotary Die Cutting Services in CA: How to Get the Best Parts
Exploring the World of Rotary Die Cutting
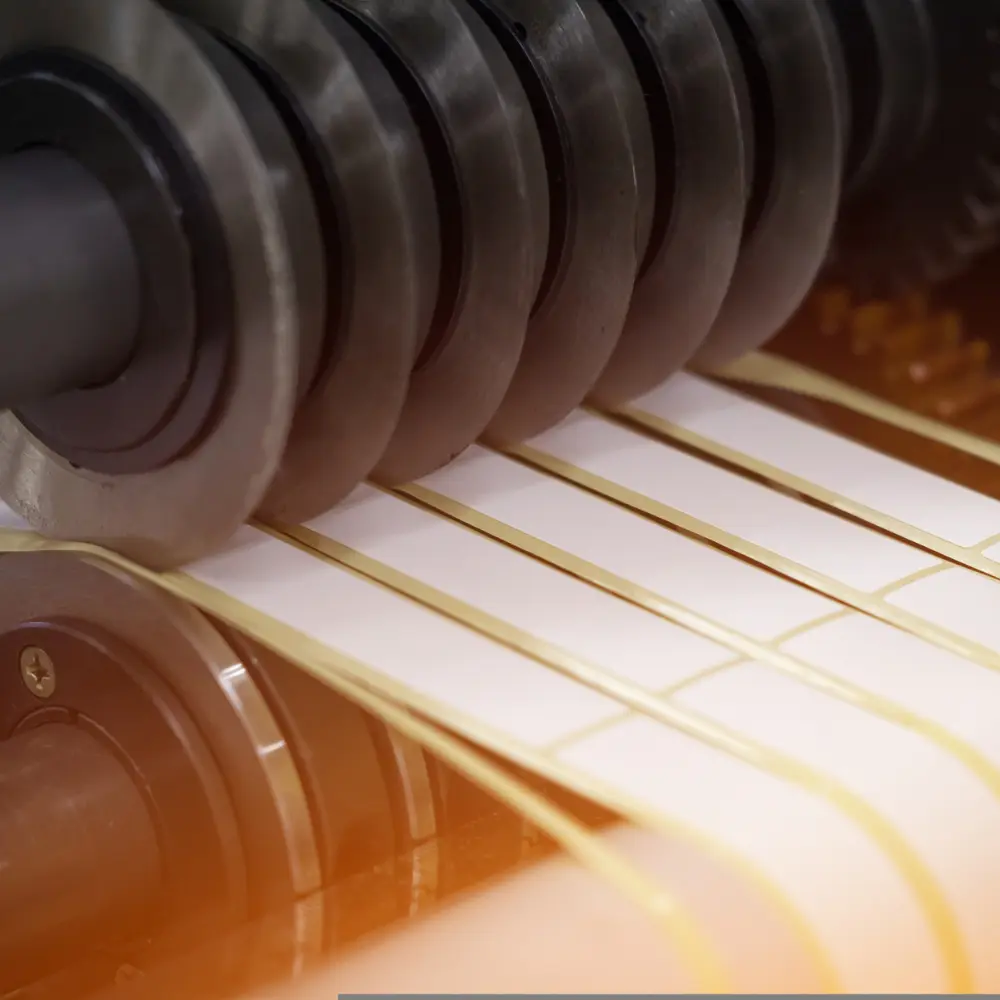
Rotary die cutting is a specialized manufacturing process known for its precision and efficiency. This process is integral to producing high volumes of identically shaped parts from rolls of thin, flexible materials, serving various industries with its versatile capabilities. At its core, rotary die cutting employs a cylindrical cutting die mounted on a rotary press to shape materials precisely. This method involves feeding a material roll, often called the "web," through the press. The web passes through multiple stations capable of converting activities such as laminating, perforating, slitting, and die cutting. Advanced rotary die-cutting setups may include in-line inspection systems and infrared light alignment to ensure unparalleled accuracy and manufacturing tolerances.
Rotary die cutting is celebrated for its numerous benefits, which include the following:
- The ability to maintain extremely tight tolerances, ensuring high precision in the final product
- Efficient material usage, leading to reduced waste
- High-speed production capabilities, ideal for large-volume orders
- The flexibility to combine several fabrication processes into a single operation, enhancing efficiency
This process can handle a wide array of materials up to 24 inches wide, with the capacity for inline laminating, slitting, and multi-material combinations, all under the watchful eye of computer-aided vision systems and inline ultrasonic welding techniques.
Material Considerations for Rotary Die Cutting
The choice of material is pivotal in achieving optimal results with rotary die cutting. Ideally suited for thin, flexible materials provided in rolls, this process accommodates a range of substrates, including fabrics, foams, silicone rubber, metal foils, and adhesive tapes. The thickness, density, and other material properties can influence the effectiveness of the die-cutting process.
Pros and Cons of Rotary Die Cutting
Pros
- Exceptional efficiency, perfect for high-volume, fast-paced production environments
- Superior precision, ideal for complex designs or parts requiring exact dimensions
- Reduced material waste through optimized cutting patterns
Cons
- Initial costs are higher due to the specialized cylindrical dies
- Material thickness and form factor limitations, with a preference for roll-fed materials
- Evaluating the Suitability of Rotary Die Cutting
To ascertain whether rotary die cutting is the best fit for your project, consider these factors:
- Material thickness and availability in roll form
- Requirement for high precision and tight tolerances in part dimensions
- The complexity of the design and the need for intricate cutouts
- The volume of production and the necessity for efficient, high-speed manufacturing
Understanding these elements can help guide the decision-making process, ensuring that the chosen method aligns with the project's specific needs and goals.
Custom Die Cutting Services in California
Rotary die cutting is a highly efficient and precise method used in manufacturing to produce custom-shaped parts from thin, flexible materials. Here's how the process unfolds, step by step, focusing on customization.
Step 1: Design and Material Selection
- Conceptualization: The journey begins with a detailed understanding of the part's requirements. This includes its intended use, dimensions, and any critical tolerances that must be met.
- Material Selection: Materials are chosen for suitability based on the part's application. Factors such as thickness, flexibility, durability, and compatibility with other components are considered. The customization aspect ensures that the material not only fits the die-cutting process but also meets the application's specific needs.
Step 2: Die Design and Fabrication
- Custom Die Creation: A custom die is designed and fabricated to match the exact shape and dimensions of the part. This involves precision engineering to ensure the die will cut the selected material accurately while maintaining the required tolerances.
- Die Testing: Before full-scale production begins, the die undergoes testing to verify its accuracy and the quality of cuts it produces. Adjustments are made as needed to ensure optimal performance.
Step 3: Preparing the Material
- Material Preparation: The selected material is prepared in roll form, known as the "web." This preparation includes ensuring the material is of the correct width and thickness and is properly aligned for feeding into the rotary die-cutting press.
Step 4: Rotary Die-Cutting Press Setup
- Press Configuration: The rotary die-cutting press is set up with the custom die. This setup includes adjusting the press for the material's specifications and the die's requirements, ensuring precise alignment and tension control.
- Multi-Station Setup: For projects requiring additional processes (such as laminating, perforating, or printing), the press is configured with multiple stations. Each station is calibrated to perform its task sequentially, integrated seamlessly into the die-cutting process.
Step 5: The Cutting Process
- Feeding the Material: The web is fed through the rotary die-cutting press. As it moves, it passes through the various stations configured for the project, undergoing transformations like lamination or perforation as needed.
- Cutting: When the web reaches the cutting station, the rotary die applies force, cutting the material into the desired shape. This process can include complex cuts, kiss-cuts, and intricate details, all achieved with high precision.
Step 6: Inspection and Finishing
- Quality Inspection: Parts are inspected for quality and accuracy using in-line vision systems or post-production checks. This ensures that every piece meets the project's stringent requirements.
- Finishing Touches: Additional finishing processes, such as weeding (removing excess material), slitting to size, or applying adhesive backings, are completed as necessary. The customization process allows for adjustments based on specific needs, including adhesive layers, creating parts ready for immediate application, or packaging for shipment.
Step 7: Delivery and Application
- Final Inspection and Packaging: Completed parts undergo a final inspection before being packaged according to customer specifications. Customization extends to packaging, ensuring parts are protected and organized for efficient use upon delivery.
- Application: The custom rotary die-cut parts are ready for their intended application, whether in electronics, medical devices, automotive components, or any other industry requiring precision-cut flexible materials.
Custom Die Cutting Services
The precision rotary die cutting process excels in producing high volumes of parts with exceptional accuracy, leveraging a range of materials and integrated fabrication processes for efficiency. Its capabilities for tight tolerances and reduced waste make it ideal for demanding projects. Choosing the right partner is the only way to unlock its full potential. Colvin-Friedman stands out as an expert in delivering custom die cutting solutions, ready to meet your specific needs with innovation and precision. Reach out to discover how we can become your trusted partner for all your custom die cutting needs.